About Hagi Ware (Hagi-yaki)
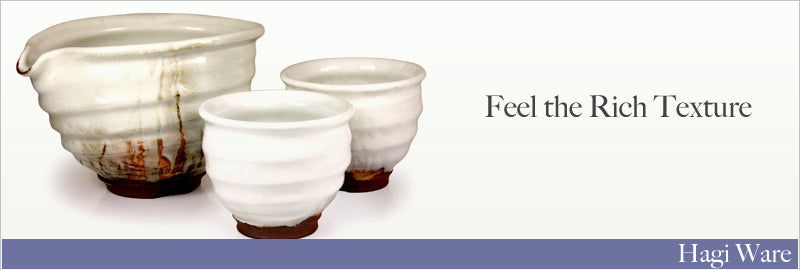
Hagi Ware

Four hundred years ago, Hagi Ware was created in Japan, through the movement of potters from Korea back to their homes in Japan. There was a battle between Japan and Korea, and during this Lord Mori attempted to protect the Korean potters in the area. However, the Japanese army won, and he moved his people to Hagi. Before long a kiln was created, and Hagi ware was created. As time when on, the Hagi style developed and changed, as more people used their creativity. Despite these changes, one similarity in Hagi ware is the softness of the clay. Hagi ware is very popular for the tea ceremony, and now Hagi ware is considered to be one of the most beautiful and most desirable kinds of earthenware in the world.
Many people do not realize that Hagi ware purposefully contains cracks which are called ‘Kannyu’. This is so that there is water permeability and ventilation in the Hagi ware, which other kinds of earthenware do not have. This means that over time, parts of the tea that is held within it move into the cracks and crystalise, giving the Hagi ware a different feel and look over time. The colors of any particular piece of Hagi ware will therefore change over time. Many people enjoy the beauty of the ever changing Hagi ware. Another reason why Hagi ware is so popular is that it manages to combine the two characteristics of simplicity with sensuousness. Hagi ware is very well respected, and the name of Hagi has entered into the Japanese lexicon and normal phrases.
Enjoying the Seven Change of Hagi Ware
The way that Hagi ware changes color over time has been given the title ‘The Seven Changes of Hagi Ware’. This is because the material used for Hagi ware is very permeable, and this allows the tea that is placed within the Hagi ware to naturally alter its color. When a piece of Hagi ware first begins its life, it is very pure and bright. However, after it has been used for a few years, the color will deepen to become more cool and calm. With even more use, the natural cracks in the Hagi ware will start to look deeper and more prominent, and this creates a totally unique pattern for each Hagi ware. The way that it is handled and used will in turn change the way that the Hagi ware will look, and so we can say with complete confidence that there is no two pieces of Hagi ware that are completely alike. When you have a piece of Hagi wear, you are helping to create a beautiful piece of earthenware that will continue to change throughout the years.
Steps in the Hagi Ware Process
1. Wedging

Wedging is the process of mixing the clay by machine. The purpose is to thoroughly homogenize the clay and to remove all air bubbles.
2. Forming

After the clay is throughly wedged, it's formed by a pottery wheel, machine and hand.
3. Engobe

The pieces are added beautiful textures to the work by using the different colored clays.
4. Drying
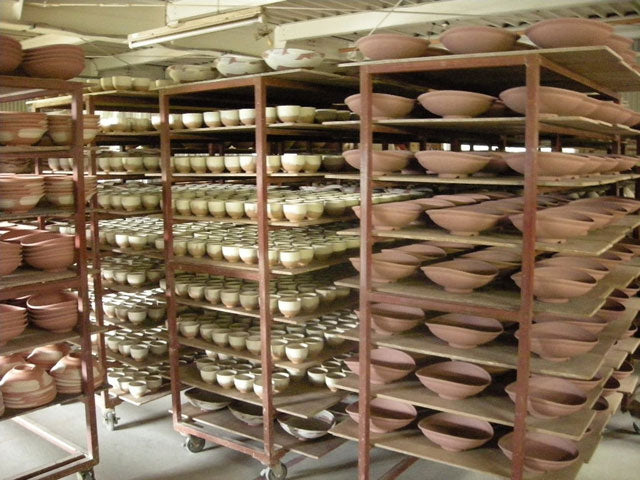
The pieces are carefully placed on the shelves. The drying process begins until the it's completely dry. Drying time depends on humidity, season and the thickness of the clay.
5. Bisque Firing

After the work has dried load it into the kiln. The firing is to approximately 1500 degrees F for 10 hours.
6. Glazing
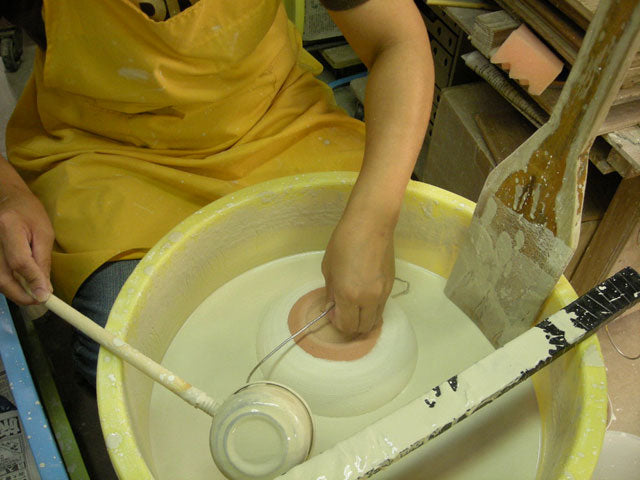
The glaze is applied to the work.
7. Accumulation

The Glazed works accumulate to fill a kiln.
8. Glaze Firing

The firing is to approximately 2200 degrees F for 12 hours in the Gas Fired Kiln.
9. Water Repellent Finish

After the firing, the Water Repellent Finish is applied to the work. This extra process is the important to improve for long-lasting.
10. Quality Inspection
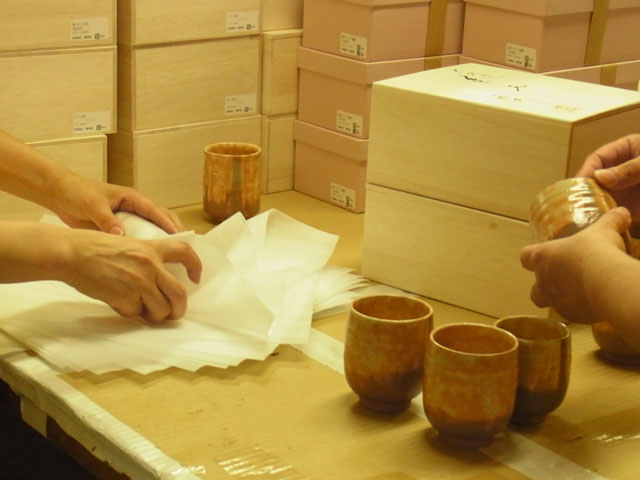
Eliminates the defective products and carefully packed into the box.